Ultrasonic Testing (UT)
Ultrasonic testing uses the same principle as is used in naval SONAR and fish finders . Ultra-high frequency sound is introduced into the part being inspected and if the sound hits a material with a different acoustic impedance
(density and acoustic velocity), some of the sound will
reflect back to the sending unit and can be presented
on a visual display . By knowing the speed of the sound
through the part (the acoustic velocity) and the time
required for the sound to return to the sending unit, the
distance to the reflector (the indication with the different
acoustic impedance) can be determined . The most common
sound frequencies used in UT are between 1.0 and 10.0 MHz,
which are too high to be heard and do not travel through air.
The lower frequencies have greater penetrating power but less sensitivity (the ability to "see" small indications), while the higher frequencies don't penetrate as deeply but can detect smaller indications.
The two most commonly used types of sound waves used in industrial inspections are the compression (longitudinal) wave and the shear (transverse) wave, as shown in Figure 10.
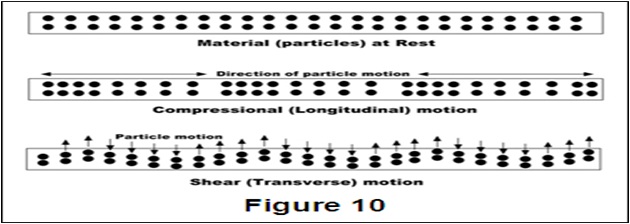
Straight beam inspection uses longitudinal waves to
interrogate the test piece as shown at the right . If the sound
hits an internal reflector, the sound from that reflector
will reflect to the transducer faster than the sound coming
back from the back-wall of the part due to the shorter distance
from the transducer . This results in a screen display like that
shown at the right in Figure 11. Digital thickness testers use the same process, but the output is shown as a digital numeric readout rather than a screen presentation.
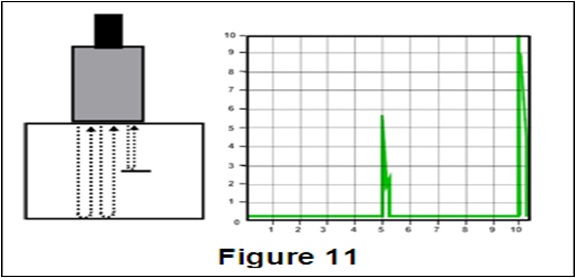
Angle beam inspection uses the same type of transducer but it
is mounted on an angled wedge (also called a "probe") that is
designed to transmit the sound beam into the part at a known angle.
The most commonly used inspection angles are 45o, 60o and 70o,
with the angle being calculated up from a line drawn through
the thickness of the part (not the part surface) . A 60o probe
is shown in Figure 12. If the frequency and wedge angle
is not specified by the governing code or specification,
it is up to the operator to select a combination that will
adequately inspect the part being tested.
In angle beam inspections, the transducer and wedge combination
(also referred to as a "probe") is moved back and forth towards
the weld so that the sound beam passes through the full volume
of the weld. As with straight beam inspections, reflectors
aligned more or less perpendicular to the sound beam will
send sound back to the transducer and are displayed on
the screen.
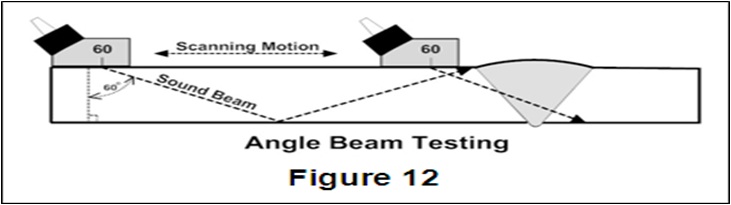
Through transmission inspections are performed using two
transducers, one on each side of the part as shown in Figure 13. The
transmitting transducer sends sound through the part and the receiving transducer receives the sound. Reflectors in the part will cause a reduction in the amount of sound reaching the receiver so that the screen presentation will show a signal with a lower amplitude (screen height).
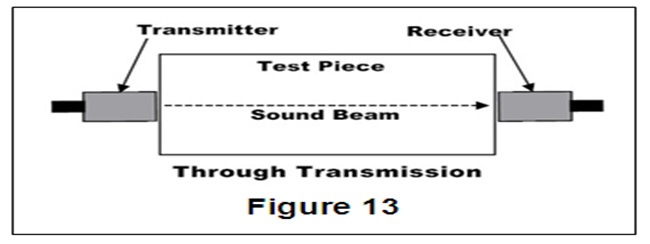